
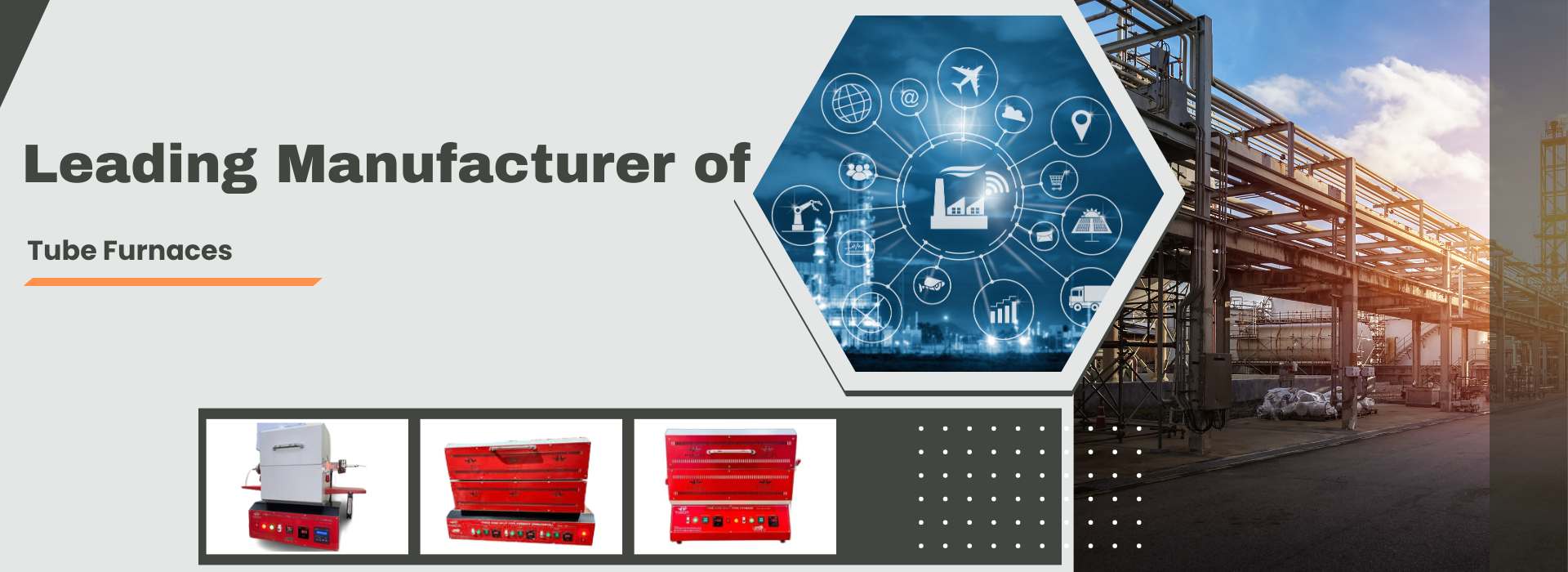
About Harrier Enterprises
HARRIER ENTERPRISES is a leading manufacturer of electric heat furnaces, lab furnaces, and Industrial furnaces in India. the company designs and sells kinds of electric resistance furnaces and provides professional solutions for customers in the lab and heat industry. Offer proof of our commitment to excellent design, quality, and cost-effectiveness.
We provide 1000°C, 1200°C, 1400°C, 1700°C, 1800°C Muffle furnace, Vacuum furnace, Tube furnace, Vacuum atmosphere furnace, Split Tube Furnace, Bottom lifting furnace, Industrial furnace, Large lifting furnace, Car bottom furnace, Laboratory Muffle Furnace, Spin Coating Unit, Industrial Oven, High Temperature Muffle Furnace, Split Tube Furnaces, Hydrothermal Autoclave, Vacuum Oven, Photochemical Reactor, and other Laboratory equipment. Our Company has passed NSIC REGD, ISO 9001 – 2015 / 14001-2015/13485-2016/FDA/ GMP/ CE Certified.
Laboratory Muffle Furnace Manufacturer, Suppliers in India
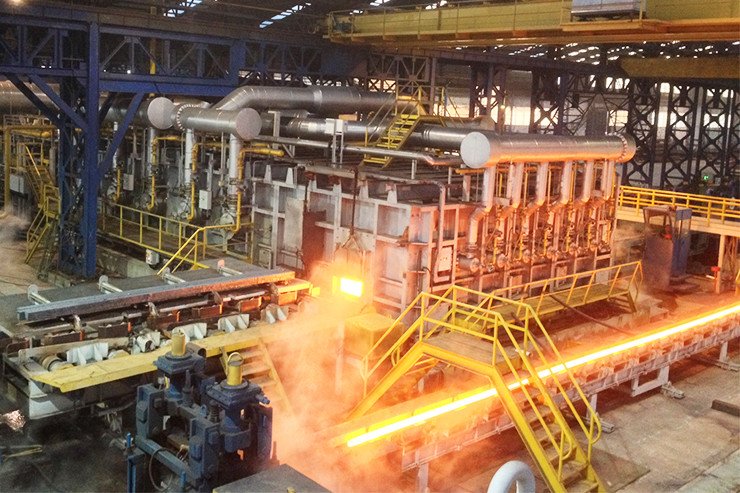
Our Products
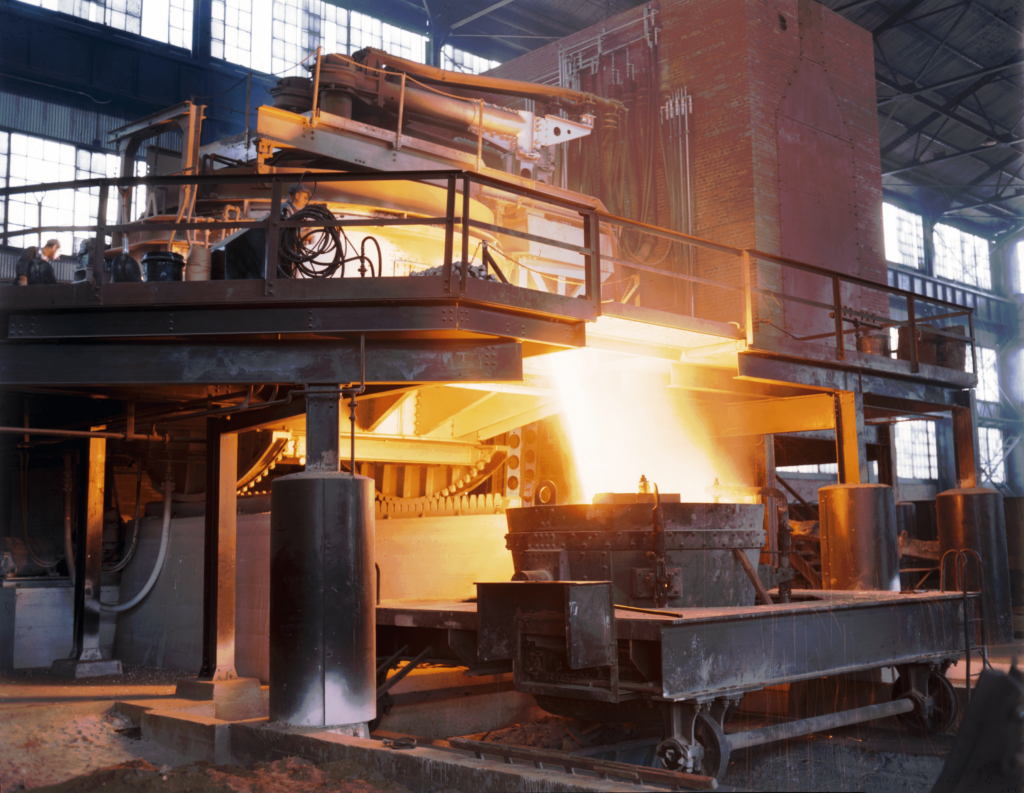
Why Choose us?
Choose Harrier Enterprises as your trusted manufacturer of laboratory and industrial furnaces for unparalleled expertise and experience, delivering tailored solutions to meet your unique requirements. Our cutting-edge technology ensures advanced, efficient, and precise furnaces, while our commitment to quality and reliability guarantees long-lasting performance and compliance with safety standards. With our dedicated customer support team, you can expect comprehensive assistance from installation to maintenance. We offer cost-effective solutions without compromising on the excellence of our products, and our global reach ensures seamless service worldwide. Make the smart choice with Harrier Enterprises and elevate your laboratory and industrial processes to new heights.
Expertise & Experience
Competitive Pricing
Cutting-Edge Technology
Quality & Reliability
Safety Compliance
Customer Support
Industries Served
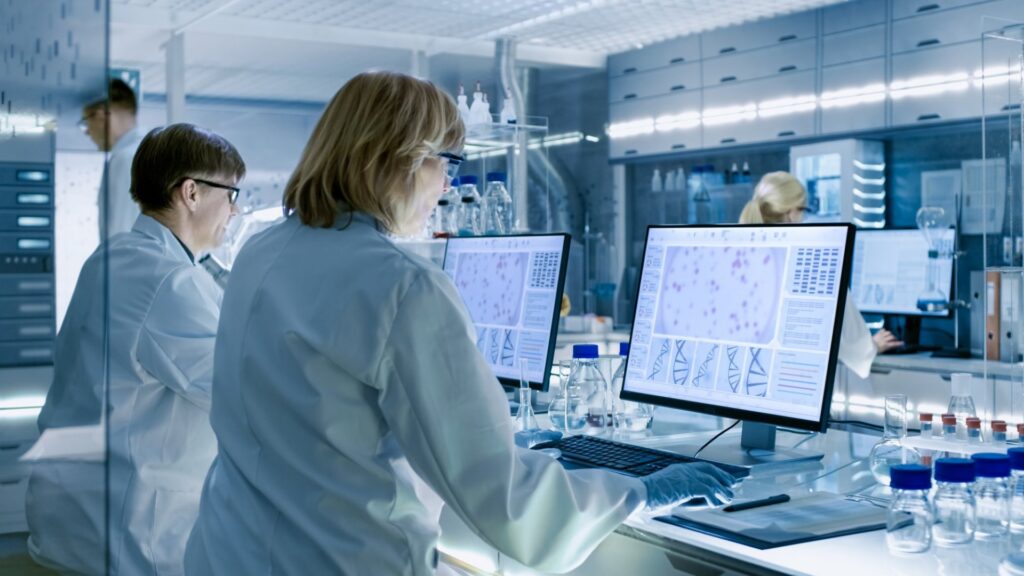
Research and Development
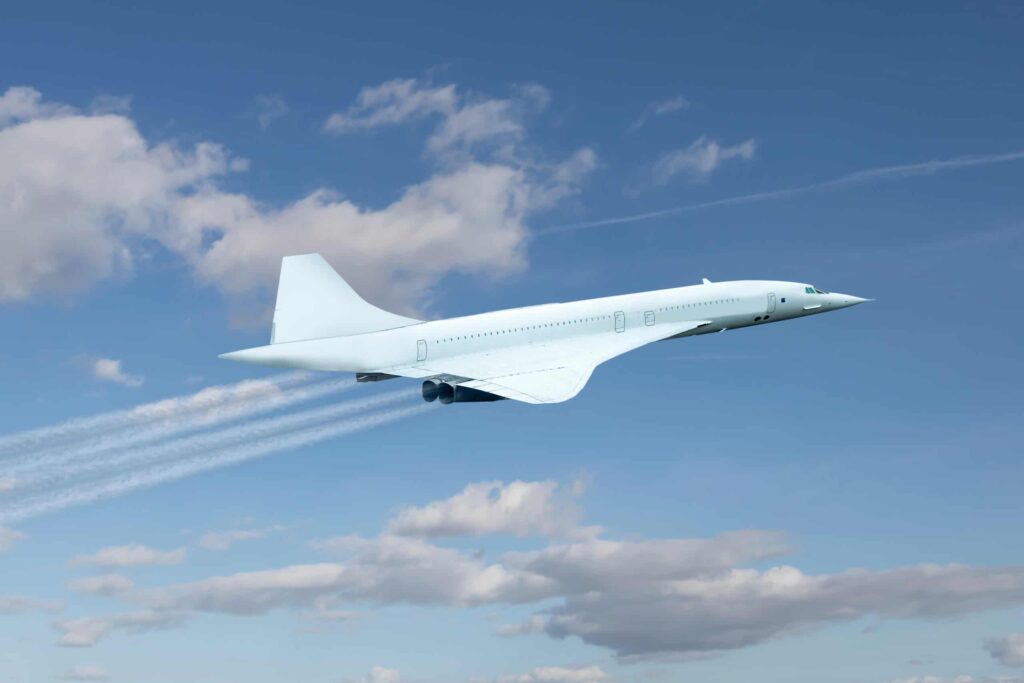
Aerospace
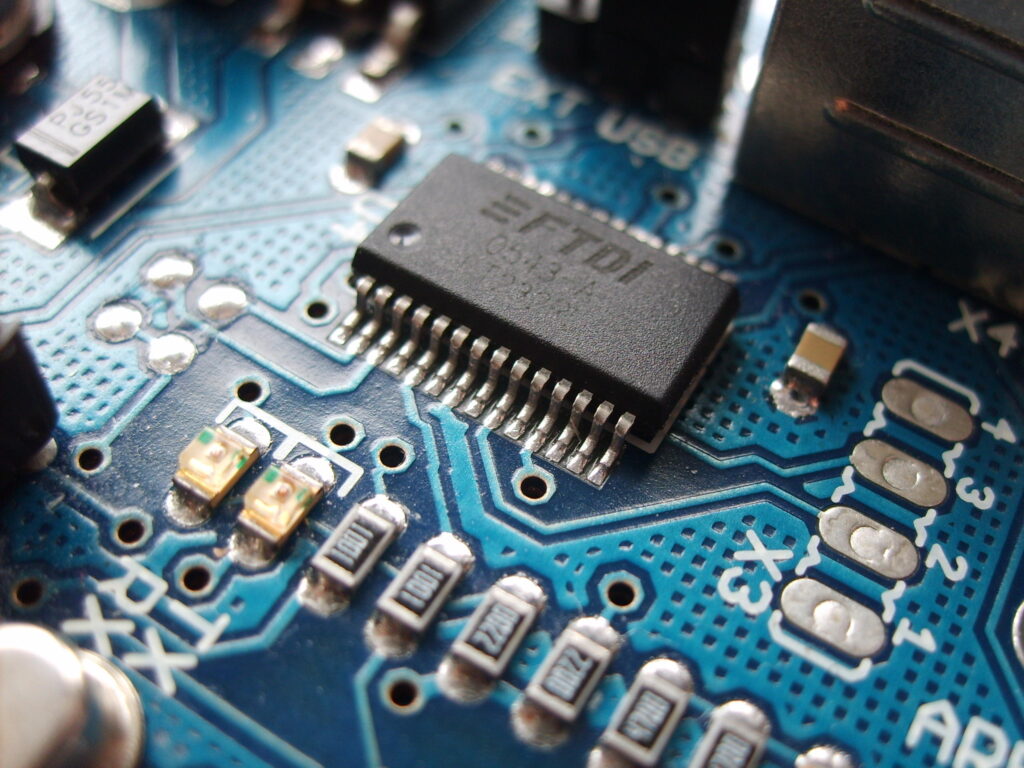
Electronics
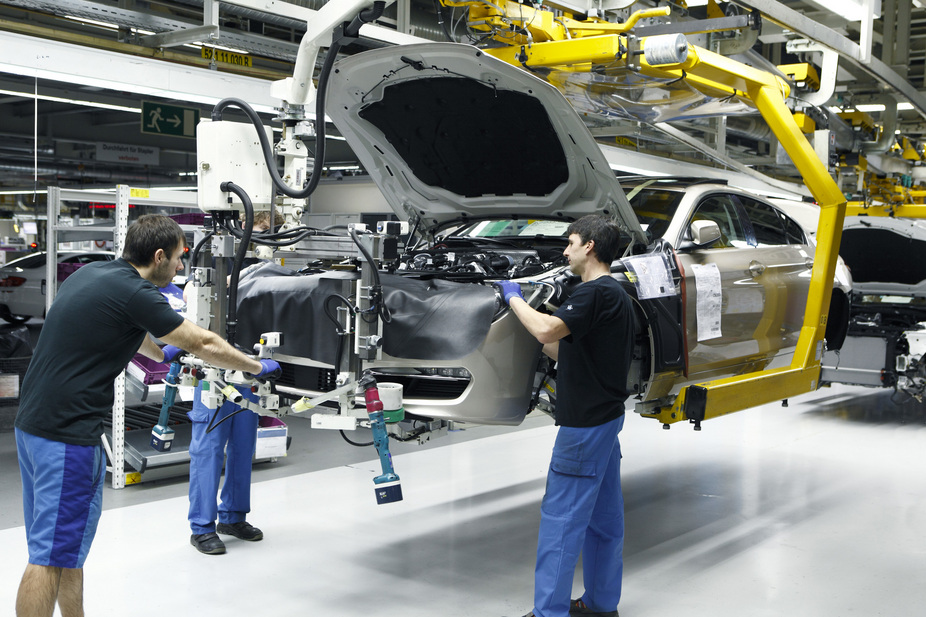
Automotive
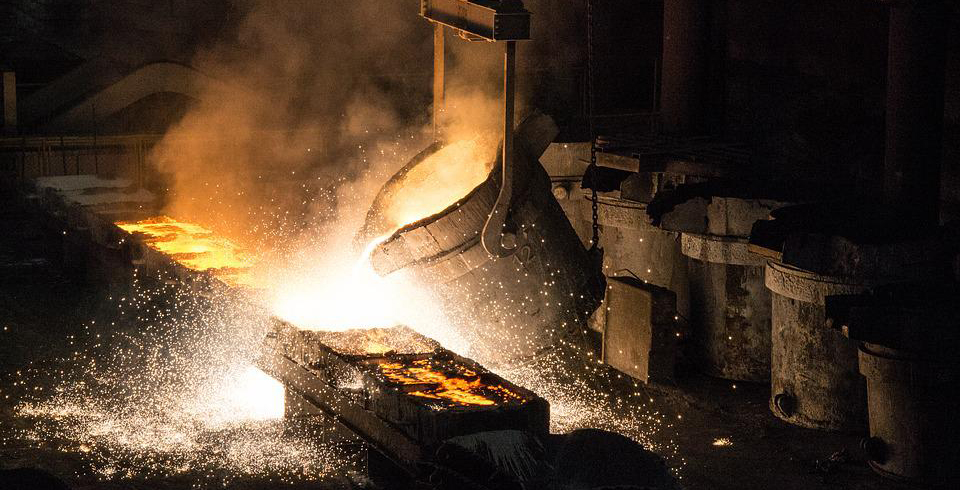
Metallurgy
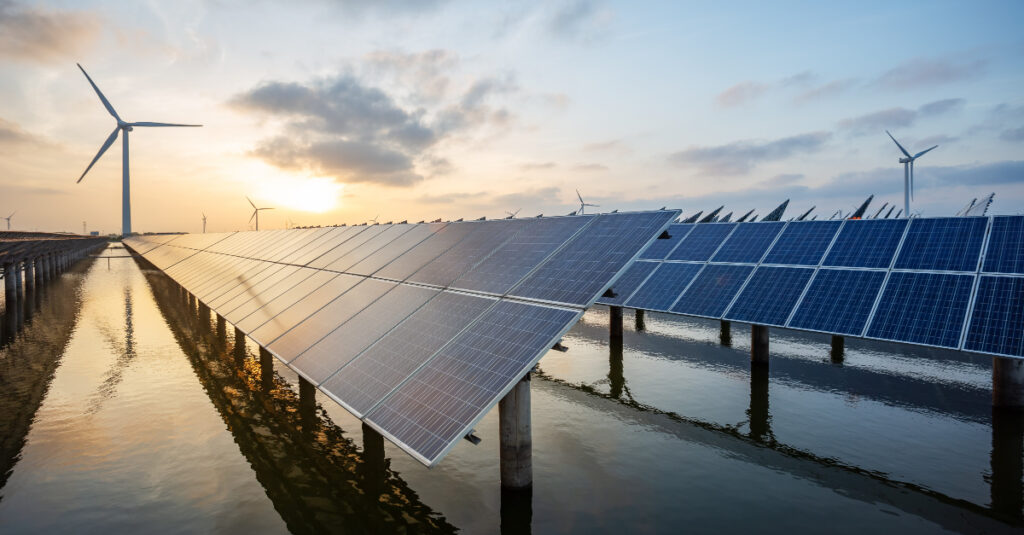
Energy
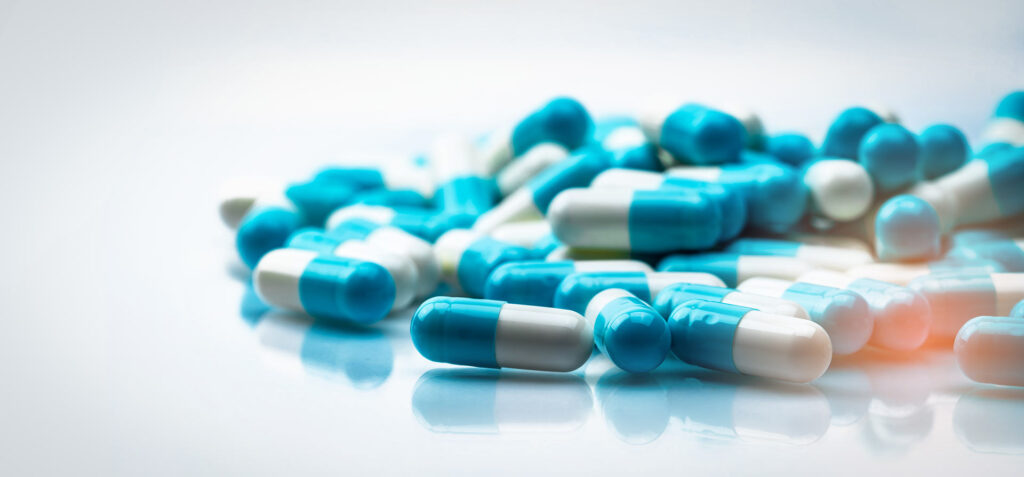
Pharmaceuticals
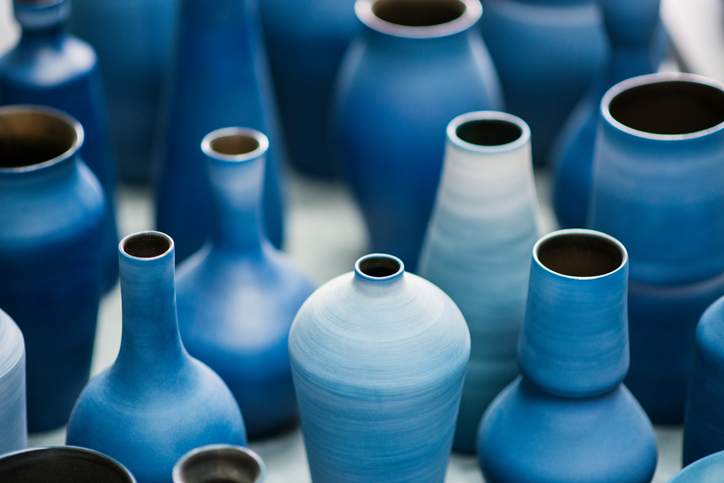
Ceramics and Glass
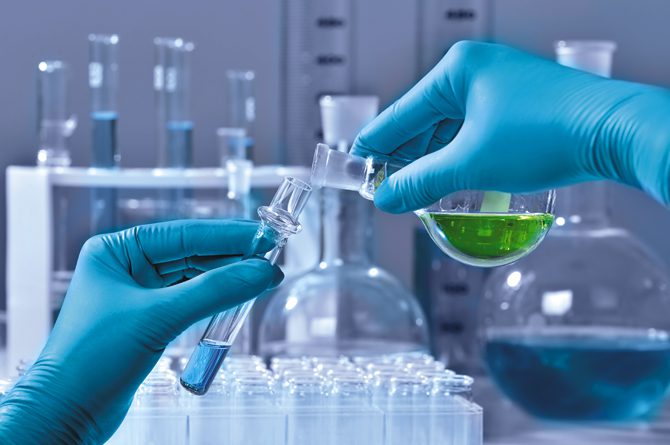
Chemical Processing
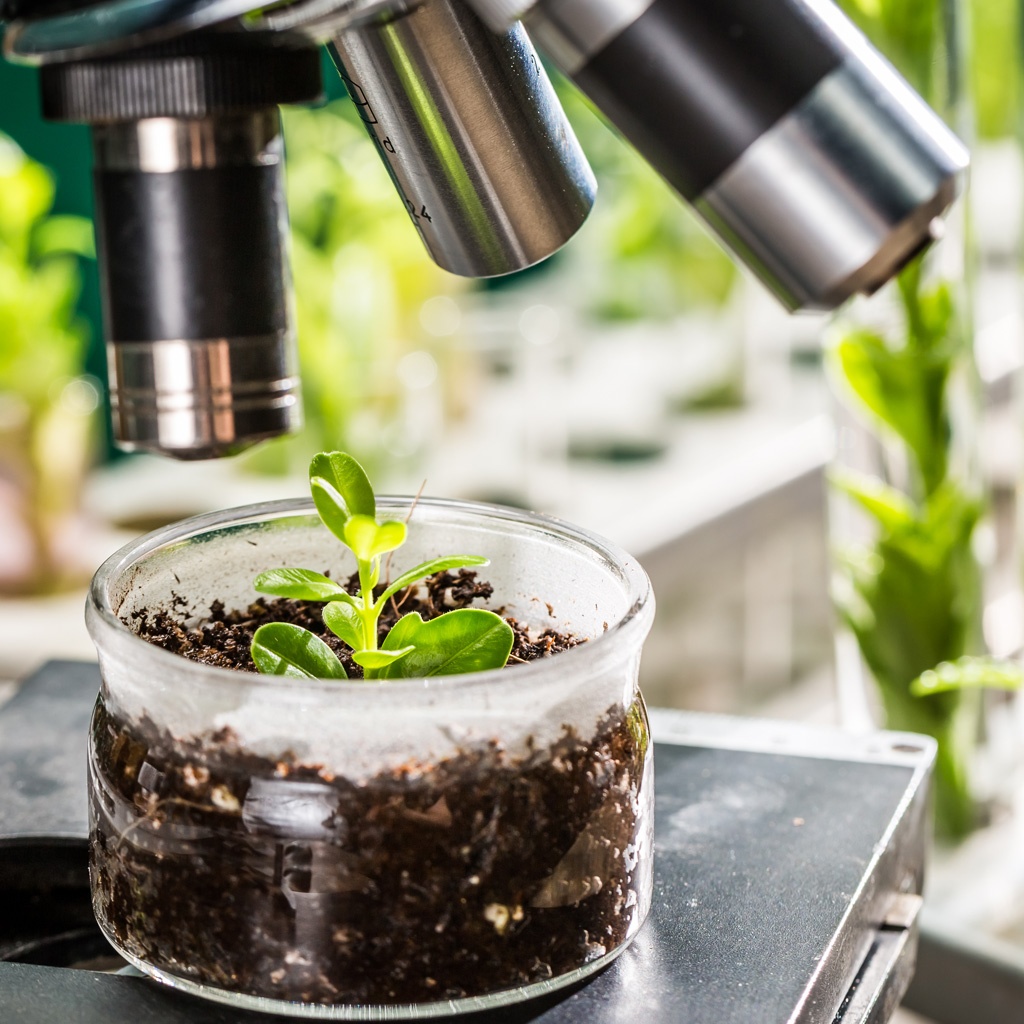
Environmental Testing
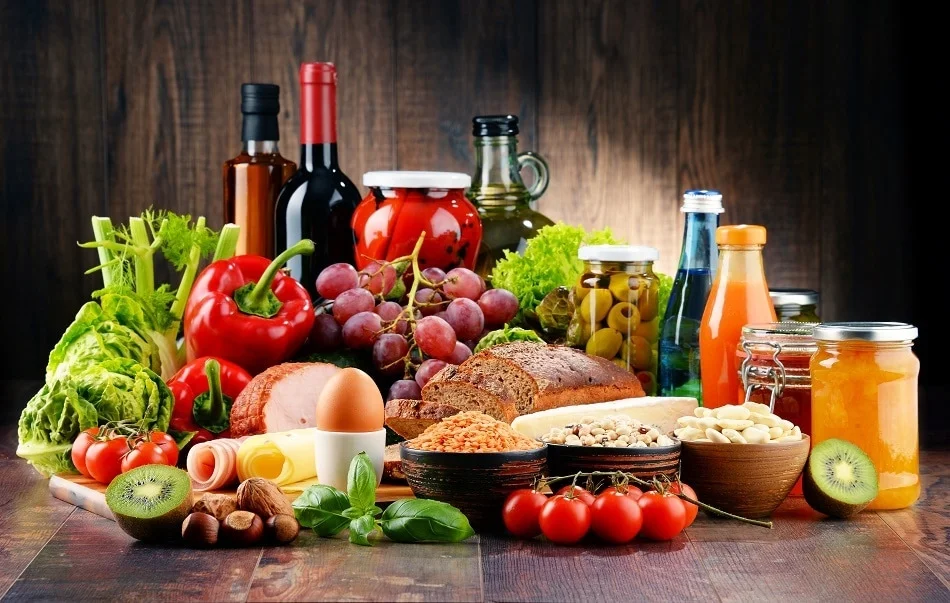
Food and Beverage
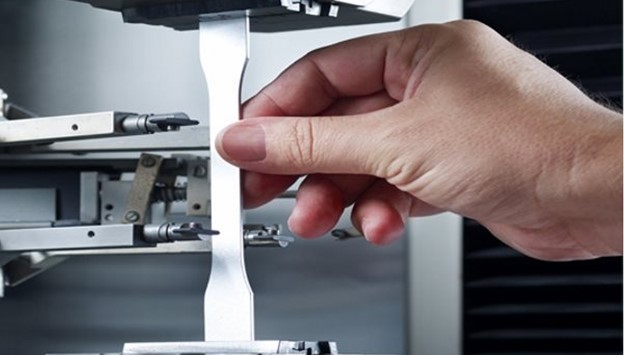
Materials Testing